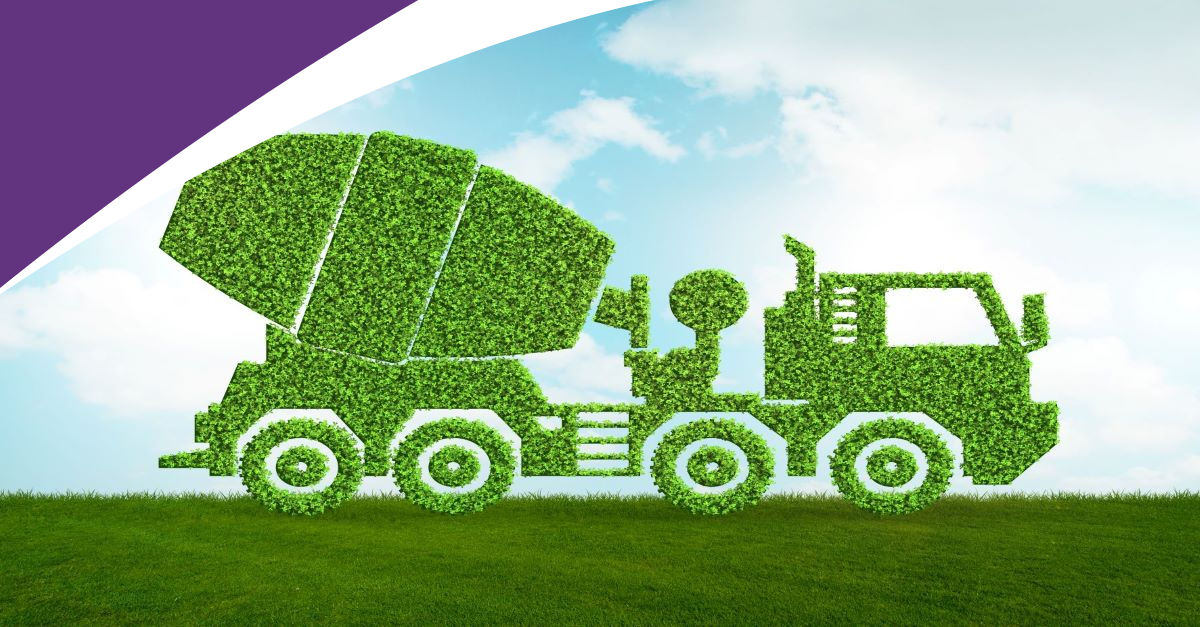
The Green Future of Construction
Like many of us, I read technical articles relating to the construction industry and I have written a few myself.
It is not often that I am startled by the contents of an article, (leastways not relating to construction), but I read recently an article by an American lady called Sasha Stashwick, a Director of Industrial Policy, Climate and Clean Energy Program at the Natural Resources Defense Council. I quote below an extract from the article:
“Concrete is the most widely consumed manmade material on Earth, used across our built environment in buildings, roads, bridges, and more. Portland cement, concrete’s common binding agent, makes up just 10-15% of the material’s mass but accounts for 80-90% of its emissions. Together, the scale at which it is used in the modern world and how emissions intensive it is to produce make cement a top source of climate pollution, responsible for about one-quarter of all industrial emissions of carbon dioxide (CO2) and roughly 7-8% of global CO2 emissions.”
My colleagues and I have worked on construction projects all over the world including projects that are “concrete intensive” including dams, bridges, causeways, roads, railways, large diameter pipelines, reinforced concrete aircraft shelters, underground command centres, concrete runways and taxiways, tunnels, culverts, even large scale housing where the key ingredient was concrete using tunnel forms to support the structures whilst the concrete cured. Add to that, the construction of reinforced concrete buildings and other structures, water and other storage tanks, manholes, concrete surrounds to pipes and a whole host of different precast and in-situ concrete products all the way down to concrete cills and lintels.
The use of cement in construction and the volumes required are dependent upon the design and the selection of materials. In my experience, cement and cement containing products is one of the most common components on every building site, large and small.
Furthermore, construction projects of any size frequently require heavy excavation and drilling equipment, portable generators, compressors, cranes, hoists and other lifting equipment, trucks, buses, cars and jeeps on large sites transporting people and materials to, from and on-site and including bulk and bagged cement and ready mixed concrete. All of them heavy users of petrol and diesel.
Not to mention or forget the cost of transporting many construction materials by land, sea and in some cases by air.
I never thought of myself as working in an industry that must classify itself as one of the world’s biggest polluters, but I have, and I do.
I read another article published by Ms. Tracey Summerell of Dentons that stated:
“Project stakeholders and the public are increasingly demanding sustainable, recyclable, energy efficient buildings that are built using sustainable construction methods and materials.”
I have read similar suggestions that environmental concerns will inevitably lead to the “greening of construction”.
Addressing the “green issues” discussed above and looking ahead, it does not take much imagination to see that in the near future, contractors’ will be required to prove and comply with environmental matters. As a direct consequence, if contractors are to avoid delays and unexpected additional costs, contract administration on all construction projects including subcontract and supply agreements are going to become more intensive; difficult; time consuming; and inevitably more expensive. In turn, that will make construction more expensive (and possibly slower) as the need to demonstrate the projects green credentials will inevitably cost more.
The risks of missing documentation, potentially slowing project approvals, payments, progress and ultimately final account settlements will be high. That must include contractors “persuading“ their subcontractors and suppliers to comply in a timely fashion with what will need to be their obligations as well.
Speaking of which, I can foresee that standard subcontract and supply agreements will need to be examined to incorporate the subcontractor and suppliers obligations on carbon issues passed on through their contracts with the contractor.
Almost inevitably, it will affect the work of architects, engineers’, contractors’, subcontractors’, and suppliers’. We may even end up with “green quantity surveyors”. (Mind you, I have met a few of those in my time!!)
I was seconded for many years on a long term basis to, at that time the World’s largest international contractor with contract values measured in billions of dollars. Initially working on very large sites in Saudi Arabia, I was appointed subsequently as subcontract manager and then contracts’ manager with overall commercial responsibility for all the contractor’s workload in-Kingdom and elsewhere in the Middle East,
In those positions, working on enormous projects, my function was a mixture of commercial and contract management. Upstream, I was responsible for ensuring that “my contractor” maximised its income and minimised its risk. Downstream, that included ensuring that any and all potential changes or delays were notified virtually immediately (refer also to my article Maximise Your Profit, Minimise Your Risk).
In that role, I was also responsible for ensuring that the subcontractors and suppliers provided to me and members of my team all the information relating to their commercial responsibilities and that also included giving of timely notices of delays and additional work.
Ultimately, on problem contracts I had to finalise the commercial aspects of the project between “my” contractor, with a variety of our clients and inevitably dealing with the project engineers.
Downstream my colleagues and I had to agree final settlements on contracts with major subcontractors and suppliers and the occasional dispute, some of which were settled amicably, some not.
As a contractor’s commercial representative and subcontract manager I would never agree a subcontractors or suppliers accounts and final payments until I had all the commercial paperwork, as I knew that if I did settle it, I would never see the paperwork. .
Thinking ahead and using my knowledge of the construction processes (and my imagination), I can only see that the administration of construction projects is going to become more time consuming and therefore more expensive. Contractors and perhaps more importantly, their subcontractors and suppliers are going to have to set up systems to manage the processes relating to the effect of construction on climate change that will be required. In my opinion that is only going to work successfully if there is a considerable amount of cooperation between the Contractor, its subcontractors and suppliers and their staff, and perhaps most importantly the Employers consultants.
Failure to manage the processes will result in delays and perhaps more disputes.
The environmental requirements will need to be set out carefully and clearly in the contracts’, subcontracts’ and supply agreements’ and someone, or some organisation ultimately will be responsible for managing what on the face of it I can only imagine will be a potentially complicated, complex, and time consuming process.
Speculating somewhat, I could foresee in the very near future the need for environmental consultants appointed on every large project who will oversee the design, selection of materials and approval of contractor selected subcontractors and suppliers.
Or am I just being green?