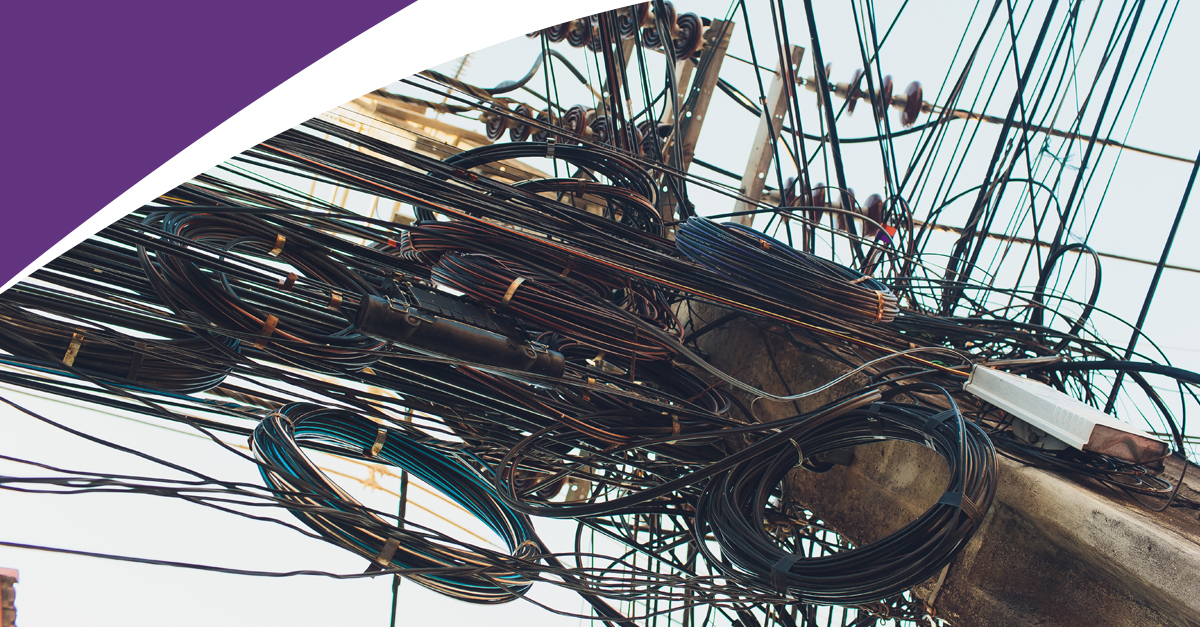
Delay and Disruption – a Separable Duo
The words of an old song run something like this: “Love and marriage – go together like a horse and carriage—this I tell you, brother, you can’t have one without the other.”
A rather old fashioned concept and one with which many people would disagree. Our language is peppered with words which are closely linked if not inseparable, including the above example.
In the construction world, we have our own apparently inseparable pair, delay and disruption. Many contractors’ claims refer to this duo as if they were one and the same thing. Considerable effort goes into analysing delay, but in my experience disruption claims are often assessed by contractors as simple percentages, or even worse; as the difference between estimate and actual cost. Sometimes, contractors present claims from subcontractors as compensation paid to a subcontractor for “delay and disruption”, in an amount that has little by way of substance to support its reasonableness, or causes.
Not only are delay and disruption completely different in terms of their separate effects on a contractor’s performance and cost, but they are reliant upon completely different records and analysed in a completely different way.
In order to understand why there is a need to decouple the two types of claims, it is first essential to understand what they are.
Delay
I define delay as an interruption to progress resulting in a contract deadline being missed. That deadline can be a milestone, a discrete part of the project, or the project completion date itself. Any part of an actual delay can result in a claim for increased “time sensitive” site overhead costs (i.e. a change in project duration will affect the site overhead costs – and in some instances off-site overheads). I include in the definition of site overhead costs, the cost of on-site management, supervision and administrative staff; on site facilities and running costs; and the cost of common plant and labour unallocated to specific activities. Not all site overheads are “time sensitive”, some are “scope sensitive”, and some are fixed. Off site, or head office overheads is a completely different subject in its own right.
Delay is measured in periods of time, principally by reference to a contractor’s programme and progress data.
Disruption
Disruption is better defined as loss of productivity of men and / or machines. Loss of productivity means that contractors pay more to achieve the same work product, or output and thereby incur a loss. Loss of productivity costs are not “time sensitive” in the same sense as site overhead costs. A delay to the project does not as a general principle affect direct labour or direct equipment costs.
Loss of productivity is measured by reference to progress data and production records.
Loss of productivity claims are much more difficult to document and prove than delay claims, which is probably why in my experience they are more often than not, misunderstood, badly prepared and presented; and sometimes badly dealt with. Enough has been written about delay analysis and I do not need to add to that debate, but loss of productivity claims are often glossed over by some authors of books and articles on delay and disruption.
Example of delay and loss of productivity
To illustrate the need to consider and present the two claim types separately, let me use the following example.
A project is divided into several different work flows, each with its own discrete work crews of direct labour and dedicated equipment. I have assumed a five-day working week.
The contractor’s “time sensitive” site overhead cost is £100,000 per calendar month. One of the crews comprising 10 men working eight hours per day has an all in cost of £2,000 per day.
The particular activity that that crew was working on is on the critical path.
On day one of that activity, Monday 1st, the crew worked normally, but, during the course of the day, started to experience material problems caused by a very late change. As a consequence of the change and the material shortages, they started to lose production.
On Tuesday 2nd, the crew again attempted to work around the material shortages, but, during the course of the day, they ran out completely and at the end of that day they still had one day’s work left to complete the critical activity.
On Wednesday 3rd, the crew was reallocated to another part of the project on non-critical work where materials were readily available and they were able to achieve their planned rate of productivity. They continued working that part of the project up to and including Thursday 11th.
At the end of Thursday 11th, the materials for the critical part of the project were delivered.
On working day 10, Friday 12th, the crew was remobilised to the critical portion of the project and, at the end of that day, completed the outstanding work on the critical activity.
The operation on the critical activity from start to finish should have taken two working days and completed on Tuesday 2nd; it was actually completed on Friday12th, a delay of eight working days, or 10 calendar days. As a direct consequence of that delay, the project ended 10 calendar days late.
The “disruption” however affected only one of several crews and only on days one and two. They achieved 50 per cent of their planned output on those two days. In overall terms, what should have taken two working days actually took three; therefore one day’s production was lost.
The costs
The cost of delay would be assessed at £33,333 (10 days / 30 days x £100,000).
The cost of lost production of the labour crew would be £2,000 (1 day x £2,000).
In summary:
- The delay of 10 calendar days was caused by a change that caused a lack of materials;
- Because of the contractor’s ability to redeploy its labour, it restricted its loss on labour costs to one day’s lost production;
- The delay would be assessed by reference to the contractor’s programme and the start and finish dates of the activity.
- The loss of productivity cost is assessed by the time taken by the labour to undertake the task compared with the estimate, or achievable production output and would be reliant upon labour records, or returns;
- Had the materials arrived sooner, or later than they did, the critical delay would have decreased, or increased accordingly, but dependent upon the contractor’s ability to redeploy its labour, the loss of productivity would be precisely the same;
- The loss of productivity did not increase, or exacerbate the delay. The critical element was the delivery of materials.
That (simplistic) example illustrates why loss of productivity, or disruption claims need to be considered quite separately from delay claims.
Records
Loss of productivity claims require extensive records. I often read, or hear about a project that was said to be “disrupted from beginning to end”. In all my years in construction, I have been involved in many projects that were badly affected by problems attributed to disparate causes that affected production, but never one that was affected in every corner of the site every day.
The real problem in my view is one of records. If contractors have a good and consistent costing system in place (and most competent contractors have) and if they are alerted to productivity problems by the monitoring process of their cost engineers, or clerks, then the sensible thing to do is to ensure that the records that are being kept are checked for completeness and passed to the commercial people on the project.
Cost reporting systems may have several purposes including:
- cost recording and final cost forecasting reports to management;
- historical data for future estimating purposes;
- establishment of claims.
All that is required by way of adequate records is a reasonably detailed work breakdown structure (WBS) that preferably is related to the progress reporting system; and the daily labour reports which identify what the labour was doing and record the hours. Pricing is simple if those records are available. If well formulated, amongst others, a cost reporting system will establish at WBS activity detail level:
- the budget (normally in hours and money);
- the production achieved in the period (normally in terms of progress percentage of an activity);
- the “allowed hours” (the hours in the estimate for that level of progress);
- a forecast to complete (in terms of hours and money).
The forecasting if undertaken properly, using subjective interrogation and trend forecast techniques alerts management to problem activities (or groups of activities) and highlights potential losses.
The budget is normally referenced back to the contractor’s estimate. Labour and equipment budgets are normally established in man, or equipment hours and money.
By monitoring the “allowed hours” and the actual hours, unusually low productivity can be identified and the commercial people alerted to any major aberrations. Enquiries to the project staff will identify the underlying reasons. If those reasons are something that is potentially compensable, then notices can be sent; records monitored closely; and any additional records kept.
All too many contractors fail to put in place adequate record keeping and fail to monitor productivity closely until after the event, by which time the ability to keep records has past. When it comes to making claims for lost productivity, they will frequently resort to global claims.
In my experience, however, the lack of composite records is not necessarily fatal to any contractor’s ability to assess and present an adequate and supportable loss of productivity claim. It will most definitely, however, make it much more difficult and expensive.
Retrospective analyses
Records
In an “after the event” situation, whether it is delay, or loss of productivity, I always start with the “art of the possible”. There is no point in providing a list of records that you would want to have, but were not kept. I always start with an inventory of what is available and/or what can be derived. The type of records that I look for include:
- the contractor’s estimate;
- details of the contractor’s costing system and cost reports;
- internal reports to management;
- ad-hoc studies and reports on profit and loss;
- labour allocation returns and all labour reports and returns;
- time sheets;
- bonus records;
- progress records and reports;
- programme updates;
- payment applications;
- any other record which will provide details of labour hours expended and / or progress achieved.
Procedures
Discussions with project staff in conjunction with project records will often be useful if not essential in identifying points of concern and filling in gaps in the document trail.
The estimate will define what the contractor expected by way of labour and equipment productivity. Hopefully, the remainder will provide, or permit the construction of adequate production outputs in respect of the affected disciplines.
If one is using the estimate as the baseline against which actual productivity is measured, it is essential to validate it to determine that the cause of loss was not attributable to a low estimate.
There are a number of ways to do this, including by reference to:
- actual production outputs on the same project by the same contractor;
- other tenders for the same work scope;
- published productivity outputs, or “norms”;
- a combination of the above.
If the records support the estimate even in part – perhaps during a period when the project was not disrupted (the so-called measured mile) – then one can either assert that the contractor was capable of executing the work at the production levels in the estimate; or that it was even capable of bettering the estimated production levels. One of the advantages of this method is that if one can demonstrate that the contractor was capable of bettering its estimate, the claim could be based upon the difference between the achievable (as opposed to estimated outputs and costs) and the actual.
Care always has to be exercised in comparing like for like, particularly using the “measured mile” technique. It must be used with caution.
Production outputs vary in different circumstances and productivity levels using the same labour force will vary dependent upon the actual circumstances. These include:
- weather;
- distance from point of entry on site to work face (particularly important on large spread out sites and high structures);
- extent of overtime working;
- bonuses;
- changes in work patterns and/or changes in support facilities, or numbers using them;
- changes in concurrent as opposed to consecutive activities;
- overcrowding;
- changes in supervision levels, or changes in labour personnel;
- perceptions of the labour force.
In relation to the above, adverse changes in weather affect the ability of labour to progress, and can and do affect productivity.
An increase in horizontal and/or vertical travel from point of entry on site to the work face will have an effect. Productivity at, or close to the ground, or the site entrance, or on-site changing facilities, will be higher than work carried out where the travel distance to the work face is greater. If it takes ten minutes to reach the workforce and assuming that the men travel back and forth four times a day; that is a loss of 40 minutes per day.
This is particularly true where the men are reliant, for example, on the use of construction lifts and hoists. Even the ability of cranes to distribute materials at great height will vary.
Estimators normally make allowances for the time taken to arrive at the workface, which is another good reason for insisting upon the examination of an estimate to check that adequate allowances were made.
Extended and extensive overtime working can and will affect production rates. Various studies have shown that limited overtime working has little or no effect on productivity per hour, but extended overtime working does have, particularly over long periods. In extreme cases, high amounts of overtime working can actually affect production to such an extent that the contractor would be better off not working any overtime. Furthermore, overtime working is more expensive per hour than “plain time” working adding to a contractor’s costs.
The introduction of bonuses ought to affect productivity as there is no point in having a bonus if it does not improve results. When comparing different production levels at different points in the project cycle, care needs to be taken to consider the effect on production of a new bonus scheme.
A change in work patterns can have detrimental effects on productivity, as can the changes in support facilities, or numbers using them. For example, the introduction of additional work gangs that are not complemented by an increase in service facilities such as generators, material distribution facilities and the like may result in productivity losses because the work crews are competing for the same facilities.
Under accelerated conditions, productivity can decrease if consecutive working in areas by different trades is replaced with tradesmen working “on top of one another”. Mistakes are made if work is done out of sequence and quite often work has to be re-done as one working trade damages the work of another.
Similarly, if too many men are added to an existing crew, but with limited work areas, the result will be the same.
Conversely, if more areas of working are opened with additional labour with no increase in levels of supervision, productivity per man can drop. Changes in supervision numbers, or even a simple change in personnel can and will result in productivity changes.
It is a belief that labour productivity will decrease towards the end of a project, or if the labour force cannot see continuity on the site and thereby perceive that they are working themselves out of a job. I undertook quite detailed research on this on a project and it became obvious from my analyses that that belief was a reality.
It is not enough therefore to simply identify that in one place a certain production target was achieved and not in another. One must consider all the pertinent circumstances that prevailed, as the increase, or decrease in production may have been down to circumstances other than something for which the employer, or contractor is responsible.
The analysis
Once the records are assembled and the work of assessing the productivity losses begins, the assessment should be undertaken in a structured orderly manner.
- Determine the actual loss (the difference between estimate / budget and actual cost) in as much detail as possible, preferably in respect of each item, or groups of items in the WBS.
- Adjust those amounts to take account of change orders to provide a like for like comparison.
- Determine if there are discrete issues that affected the loss, assess these separately and adjust the affected costs in each element of the WBS.
- Establish the achievable production either by reference to a verified estimate, or by reference to established production norms, or using subjective analyses of production achieved elsewhere (the “measured mile technique”).
- Divide the project into comparable areas or work flows.
- Establish common comparators by establishing production outputs in simple measurable units that permit simple comparisons (e.g. square metres, or weld inches) in respect of each of the areas, or work flows being considered.
- Establish the productivity levels and costs per square metre, or suchlike of the various areas, or work flows and compare them.
- Identify the most productive of the areas, or work and establish efficiency levels in respect of each.
- Establish the unexplained productivity losses (e.g. see Table 1 below).
- Determine the timing of the losses in relation to the actual programme.
- Look for the possible causes of loss by reference to identifiable events.;
- Link possible causes to the production losses.
- Finally, apply intelligence to the results, preferably with the existing site team.
- Establish the loss of productivity losses attributable to the various parties.
One I prepared earlier
Table 1 below provides a summary of the results of a detailed study on a project where I was instructed to examine the “disruption” claim prepared by a claims consultant.
Using many of the techniques described above, I established the actual manhour expenditure of 16 different work flows, using measurements of areas of finished work in respect of three disciplines to assist in establishing common comparators.
Secondly, with the assistance of the project staff, I identified three discrete issues that had increased the costs of labour. I assessed these costs separately and removed them from the overall costs of the different work flows.
Thirdly, I compared the residual actual man hour expenditure and the resultant costs with the estimate.
Table 1 (in summary form below shown in programme sequence) provides an indication of the results for one of the disciplines.
I plotted the results on a time line and compared the results with the events that had occurred on the site.
After examining and analysing project records and following detailed discussions with the project staff, I was able to measure productivity efficiency on each of the work flows and link them to events which had occurred on the project. Subsequently, I was able to link quantified losses to specific events that that were attributable to employer cause.
Percentages of 100 per cent or above indicate that the contractor was achieving a productivity level at, or higher than its estimate which it did in 10 of the 16 workflows and less in 6. I noted in particular the results from work flow 1, which was the first work flow in the construction sequence, and work flow 5 which produced the best results. Work flows 15 and 16 achieved the lowest productivity.
Table 1: Productivity assessment
Work flow | Productivity / efficiency (%) |
---|---|
1 | 115 |
2 | 100 |
3 | 97 |
4 | 100 |
5 | 123 |
6 | 102 |
7 | 92 |
8 | 100 |
9 | 108 |
10 | 95 |
11 | 111 |
12 | 99 |
13 | 105 |
14 | 106 |
15 | 81 |
16 | 57 |
One of the key features in my assessment, I concluded, was the lack of continuity and available work fronts. As the labour force perceived a lack of continuity, the productivity decreased; as the perception of future work improved, productivity rose. There were particular difficulties on this project relating to the inability of the contractor to react to events by demobilising and remobilising labour that exacerbated the problems and increased its loss.
Fluctuations in productivity were evident shortly after the beginning of the project when a lack of continuity became evident in the finals stages of work flow 1. As a consequence, productivity levels dropped in flows 2 and 3. They improved in flows 4 and 5 as the initial continuity problems were resolved, but declined after flow 5 as further problems were encountered.
After that, the productivity levels ebbed and flowed as further problems were encountered and various measures were taken to circumvent them. Finally, towards the end of the project, the productivity plummeted as, at a time of high unemployment, the labour force could see clearly that it was working its way out of a job.
Referring to my comments above concerning the measured mile, I had verified the original estimate by means of these analyses.
I concluded that not only was the contractor capable of achieving its estimate in terms of man hours and cost, but the results from the very first work flow indicated that it was capable of achieving a higher than estimated level of productivity and thereby a lower cost on day one.
In this instance, I felt justified in using a base production and cost measurement value lower than the estimate by using the actual production results of work flow 1 and 5 as the benchmark against which to assess the achievable production levels of the other work flows and thereby establish losses.
I repeated this analysis for two other disciplines and they indicated markedly similar results. There were specific exceptions, where particular and identifiable circumstances had affected their productivity levels, but the results of those other analyses confirmed my opinion and my assessment of loss.
Cause and effect
Loss of productivity assessments are seldom easy. They do require a considerable amount of analysis and work to identify and quantify the losses and to link those losses to events that may be attributable to another, and thereby compensable.
It is not possible however to link every single loss to every single loss making cause. It might be possible to link a major loss of productivity to a single event, such as a complete cessation of activities, or so-called “idle time”. Idle time is simply an extreme example of productivity loss.
In my experience, loss of productivity assessments are almost always going to be approximate and more often than not assessed by reference to more than one event. As with all analyses, whether it is delay, or loss of productivity, any calculation requires what I call “the application of intelligence” to ensure that the results not only look sensible, but are both sensible and defensible.
From the example highlighted above, it may be evident that validating an estimate, or assessing an “achievable” level of production, or efficiency, comparing that with actual production achieved and linking that to employer responsible events assists a tribunal to assess measurable and discrete losses.
This type of analysis, however, requires records that the average employer, or the contractor defending a disruption claim brought by a subcontractor will almost certainly not have. It can only be done by the contractor. Any employer is therefore disadvantaged if a contractor has not undertaken an appropriate analysis. I address this below.
Settlements with subcontractors
With reference to subcontractors, many contractors will agree “delay and disruption” claims with their subcontractors as a composite “commercial deal” and then present the agreed amounts to the employer for payment.
First, I would certainly urge any contractor to ensure that it extracts sufficient information and records from the subcontractor before it settles.
Secondly, to make sure that it keeps a complete record of any negotiation.
There will inevitably be a point in a negotiation where the parties have each carried out some form of analysis; negotiations will reduce the gap perhaps with some reasoning; and finally a “deal” will be done cutting the final figures at some point in between the two figures.
One can criticise contractors for settling with subcontractors and attempting to pass on the results to an employer, but the reality is that on a live project it is sometimes more essential to settle matters and move on, rather than allow festering dispute to sour relations and progress.
In situations where a deal has been done with a subcontractor, I adopt a self-interrogation technique asking myself three questions:
- Was the amount paid?
- Is the amount linked to events for which the employer is responsible?
- Was the amount agreed reasonable in all the circumstances?
If the answer to any of the questions is no, then I examine it further to determine figures that I would be able to support.
Global loss of productivity claims
If the contractor bringing the claim does not make its records available, then the person, or organisation seeking to respond to the claim and assess its liability (if any), or at the least to minimise its exposure, is disadvantaged as it cannot prove a negative. The contractor or subcontractor may even assert that the records do not exist.
In the event that a global disruption claim is pursued, the responding party may have no real means at its disposal to disprove, or challenge it. Whether retained as an expert by a claimant, or a respondent, I adopt the same level of rigour in my examination of a disruption claim. Before I would be prepared to accept that a global claim was the only way of assessment, I would need to be satisfied that all possible records had been examined and no stones left unturned to ensure that a more particularised claim was not possible. In any report prepared by me, I consider that it would be incumbent upon me to document the steps that I had taken to do better than provide a global assessment. Furthermore, if there was clear evidence that there were contractor inefficiencies, these would need to be identified and assessed.
However, in my experience, not all “independent” experts are as objective as they ought to be and they may not adopt the same degree of rigour as some of us that are.
A tale of two awards
I have seen a tribunal’s decision which awarded a contractor a percentage of its costs over and above costs that it would have incurred. The hearing was bifurcated (i.e. first liability then quantum). The first hearing focussed on delay issues. After the first hearing on liability, the tribunal judged delay and disruption effectively to be one and the same thing and the percentage was to apply not only to delay costs, but also the claimed additional costs of labour. That percentage as far as it related to loss of productivity was arrived at in an almost complete absence of any information, or evidence on quantum.
In my many years of working on sites and as an expert, I simply could not arrive at a percentage of loss of productivity without some evidence of linkage and some indications of the extent. In my opinion, guesses involving substantial sums of money are simply not good enough.
Sitting as an arbitrator, or adjudicator, I would expect the claimant to demonstrate the measures taken in its attempts to particularise its claims.
Global warning
By way of contrast, I gave evidence in an arbitration where I was appointed by a Government agency to provide an expert report on quantum. There were substantial claims for “disruption”.
The claimant had not only neglected to provide meaningful support to its disruption claims, it refused to provide to me any access to its cost records.
My evidence concluded before lunch on the last day of the hearing. I was the last witness.
After lunch, the chairman addressed the parties and flagged up the tribunal’s concerns at the global claims put forward by the claimant and I quote:
“Here I would like to just share with you we are having some problems with that claim put forward as a global claim.
We have some problems with that claim from a conceptual legal point of view. I refer you simply to the causation issue, and within the context of a global claim we have some problems with the calculation of that claim. So you should be aware of those issues when you address that claim, particularly this applies to the Claimants.”
In its award the tribunal decided the following:
“Moreover, (the Claimant) do not appear to have made a reasonable attempt to address this problem. Whilst insisting on making a ‘global claim’, (the Claimant) have refused to provide their original contract estimate based upon which their global claim could have been assessed, despite requests by (the Respondent) and its quantum expert Mr. Wishart that they do so and the Tribunal’s warnings regarding their ability to prove their damages should they continue to refuse. (The Claimant) have also not provided any evidence to substantiate the time that they allege their staff spent, whether by providing access to their electronic timesheet system or hard copies of timesheets, again, despite requests by (The Respondent) and warnings from the Tribunal.
In sum, (the Claimant’s) claim entirely lacks the requisite substantiation. This conclusion is also supported by the findings of Mr. Wishart, (the Respondent’s) quantum expert, who reviewed the documentation provided by (the Claimant) in support of the quantum of their claims and who concluded that they were not supported in any meaningful way (Wishart I & II §17).Under these circumstances, absent any evidence to demonstrate a connection between the additional manhours spent and the additional work for which those hours were allegedly spent, the Tribunal must reject (the Claimant’s) claim.”
In an instant, some $32 million of claims were denied. A sobering tale for any contractor submitting a global claim.
Summary
- Delay and disruption (loss of productivity) claims are not linked, but quite different.
- They rely upon different records and they are analysed in quite different ways.
- Loss of productivity claims are difficult to document, assess and prove.
- As a consequence, they are often presented as global claims of loss.
- Contractors are advised to keep good meaningful records.
- Establish an inventory as to what records are available.
- Contractors ought to make every effort to particularise their claims, or prove that they cannot.
- Known periods of contractor inefficiency need to be identified and quantified.
- Respondents ought to demand that a contractor’s estimate, internal cost reports, progress records and all necessary records to permit the evaluation of loss of productivity claims are made available to it; and tribunals ought to warn of the consequences if they do not.
- Claimants submitting global loss of productivity claims might get away with it, but it is a high risk strategy to assume that it is going to get something out of a global claim. It may well end up with nothing if it faces a robust tribunal.
Finally, I tell you, brother, in relation to delay and disruption, you can (and do) have one without the other!